Locomotive Specifications
8783 'Phoenix' will be built to the D16/2 original 'super Claud' specification, with additional modifications and upgrades. Such as improved lubrication and improving maintenance. We intend to fit the locomotive as per the royal LNER specifications, with the brass funnel and increased level of brass work.
D16/2 had a total working weight of 94-3-0 tons, max working pressure of 180lbs per square inch and a tractive effort of 4.76.
Below is a full engineering breakdown of a D16/2. All information supplied in imperial units, unless noted in brackets.
Wheel size:
Bogie - 3ft 9inch 4 No. of
Driving - 7ft 4 No. of
Tender - 4ft 1in 6 No. of
Boiler information:
Boiler barrel - 11ft 9in lg x 5ft 1.125in dia
Firebox outside length 7 ft
Total grate area of 21.6 sq ft
Boiler pressure of 180lbs per square ft
187 small tubes and 21 super heater flues
2 Ross pop safety valves
Cylinder and motion information:
2 No. cylinders 19 inch dia x 26inch stroke
Inside cylinders
Horse power per cylinder 1169
Stephenson slide valve motion
Tractive effort at 85% 17096lbs
Total adhesive weight 81312lbs
Total tractive effort of 4.76
Locomotive size:
Overall buffer length of 53ft (16.1m)
Overall width 8ft 8 inch
Overall height 13ft
Loco length 32ft 3 inch
Tender length 20ft 9 inch
Locomotive weight:
Loco weight when loaded 54-18
Tender weight when loaded 39-5
Total loaded weight 94-3 tons
Tender information:
Standard GER tender
5 ton coal capacity
3450 gallons water capacity
Water scoop (not fitting)
Raised coal guards
Well tank
General information:
Westinghouse brakes
Vacuum ejector
Route availability 5
Power class 2P (D16/3 3P)
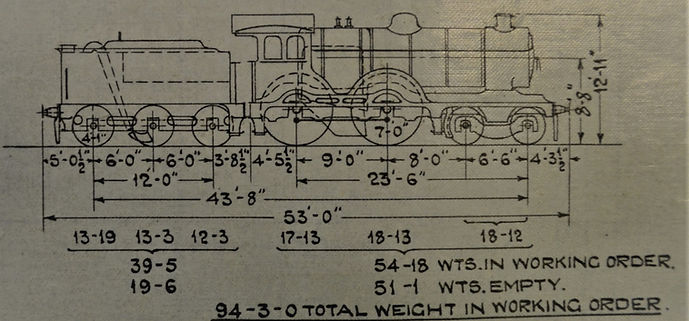
The group plans to make some changes to the D16/2 design by incorporating some ideas and improvements made to other engines. Some ideas have been listed below.
Like all engines curtain areas need to be cleaned out after use, the smoke box and ash pan being the main areas. The engines suffered with ash falling and getting onto the motion and important moving parts. Information supplied to us by an Ex British rail fitter. We will be undertaking improvements to how the engines are cleaned out and stopping the ash from falling through. Inspection lights in key areas will be installed for maintenance during night time preparations or early morning preparations.
Temperature gauges will be added near and on working parts, which will supply the crew continuous updates of the temperature. This will look to eliminate any future serious damage coursed by poor lubrication. Also increasing the size of oil pots and number of pipes to those oiling points, improving the length of time running and stopping any blocked pipes.
We will also look to make duplicate parts for important motion components and well used parts, lowering the down time of the engine between overhauls or during serious maintenance.